3D Printed Composites
3D printed houses, metals and glass are some of the latest innovations in 3D printing technology.
Large scale 3D printed structures are becoming increasingly popular. In 2016, the world’s first 3D-printed office was produced in China, then assembled and finished in Dubai. In 2019, Icon, a Texas-based start-up, created the first 3D printed community in Tabasco,Mexico. Icon has also printed houses in Texas. Icon uses a proprietary cementitious mixture called Lavacrete in its printer. Icon’s 3D printers can create a 500 square foot house in 24 hours (Glover, 2019). Apis Cor, a Russian company, was also able to produce a 400 square foot house in 24 hours in 2017 for $10,134 USD (Sakin & Kiroglu, 2017).
Stereolithographic 3Dprinting processes can use sand, various aggregates and an inorganic binder to create structures such as 3D reefs.
Large-scale 3D printing robots print using varied mixes of granular materials, binding agents and fibres. The binding materials that solidify the shapes can be composed of either an aqueous or cementitious solution. A material called Laywood is a wood and polymer composite specifically developed for 3D printing applications. Polylactic Acid is a biodegradable polymer which is growing in popularity due to its ability to be used in 3D printers (Sakin & Kiroglu, 2017).
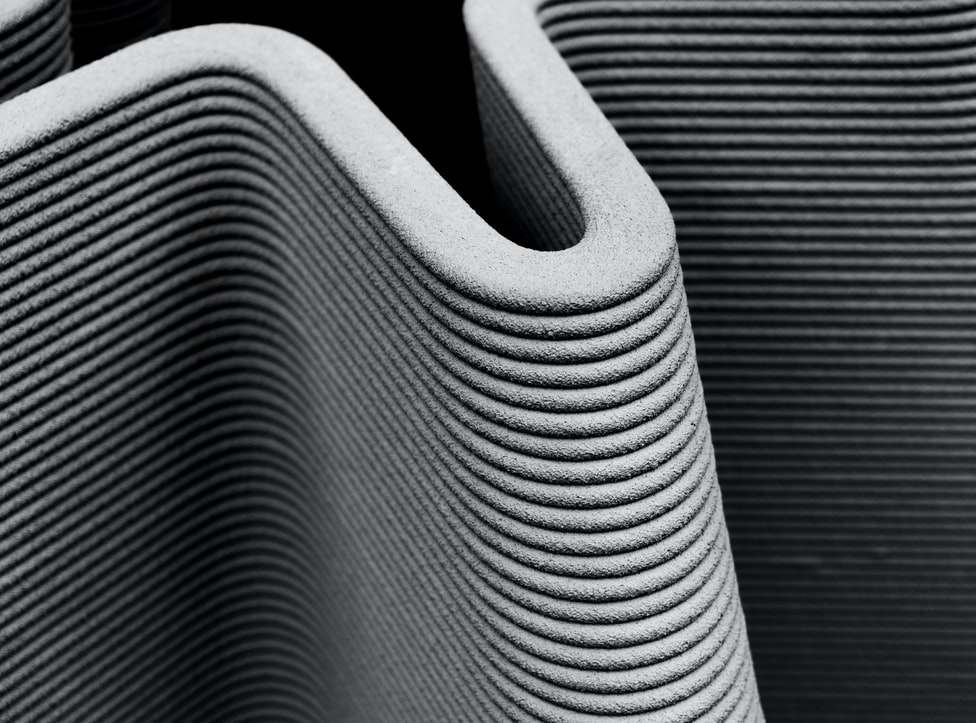
Benefits and Drawbacks
No formwork or reinforcing is required for these structures, some of which can cure within 24 hours. This particular method of construction is able to construct structures in any shape. One of the patented printers by Monolite UK – registered as “D-shape”—has been used to create artificial reefs as well as houses .
3D printed buildings have been shown to reduce construction waste by up to 60%, and reduce labour costs by up to 80%. In addition,according to the United States’ Survey of Construction from the Census Bureau,a production house takes an average of 4-6 months to build, and a custom house takes 10-16 months. In comparison, Dubai’s 3D printed offices were built and custom-finished in 3 months.
The drawback of this method is that there are currently few companies with 3D printers large enough to produce large-scale 3D printed buildings. Icon’s 3D printer is 33 feet long and can print a house with a footprint of up to 2000 square feet. Monolite UK has printed similarly sized structures.
Commercial Readiness
Firms currently commercially produce buildings and building components. For instance,Monolite UK Limited has collaborated with universities such as TU Delft, TU Eindhoven, ETH Zurich, MIT, Harvard, TU Munich, and architectural and engineering firms such as Foster & Partners, ARUP and Zaha Hadid Architects to create buildings. Icon has produced 3D printed communities, and the structural capabilities and durability of the structures will be monitored in the coming decades (Glover, 2019). AONIQ is an Australian firm which 3D prints pipes and pipe fittings for commercial use (Petch, 2017).
Cost Analysis
3D printed buildings have been shown to reduce construction waste by up to 60%, and reduce labour costs by up to 80% (Sakin & Kiroglu, 2017). According to the United States’ Survey of Construction from the Census Bureau, a standard house takes an average of 4-6 months to build, and a custom house takes 10-16 months.In comparison, Dubai’s 3D printed offices were built and custom-finished in 3 months. Apis Cor, a Russian company, was also able to produce a 400 square foot house in 24 hours in 2017 for $10,134 USD (Sakin & Kiroglu, 2017).
For pipe printing, PVC filament is priced at $1,490 for 10 rolls on the AONIQ website,and the AONIQ 888 printer costs $10,499 USD.